There seems to be a lot of "common
knowledge" out there for the TC3 that's not written down anywhere.
That's the point of this article. So let's get up on it.
The first thing to remember about your TC3 is the chassis can
get tweaked easily. Most of the time the motor is left in the
car hot. The chassis will take a tweak from the tension of the
motor mount screws. It's really important to at least loosen up
the screws before you do anything else after a run (i.e. marshal,
return transponders, etc.)
The best thing to do is to pull it completely out. Another heat
related item to look for is a protrusion in the bottom of the
chassis. The bottom of the motor cam pushing through the chassis
when it gets hot causes this.
You
want to remove a portion of the material from the bottom of the
motor cam. The picture will give you an idea of what to do. Basically,
you're just looking to remove enough to stop the protrusion from
forming and creating a tweak in the chassis.
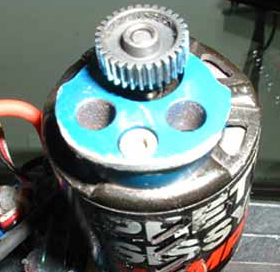
The driveline needs attention as well to get the maximum out of
it. Some of this can be easily screwed up, so do not do it if
you are not sure you want to. It's really for obsessive people
like me who need lives. Besides, I won't shell out for new parts
for your car anyway. A "bearing blaster" type device can be used
to flush the grease from the bearings.
They can also be soaked in motorspray or other solvents. Basically,
the grease is too heavy, and slows things down. Some guys like
to remove 1 or both seals from all of the bearings. I just remove
the inside seal from the large outdrive bearings and leave the
seals on the rest of the smaller bearings. You can use a fresh
razor blade to extract the c spring holding the seal on. Mobil1
motor oil 0w30 is cheap and excellent oil for bearings. There's
a lot of other stuff like Niftech, Prolong, etc. Use what you
like as long as it's light. I like to soak the bearings in the
oil, and them let them drain overnight on a paper towel. I spin
as well to get the excess lube out. All 8,000,000 other techniques
are just as valid, I'm sure.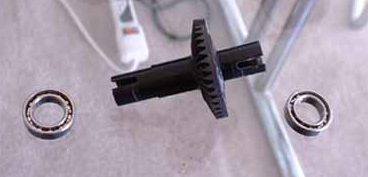
The pictures show the areas of the trans housings that need to
be carefully gone over. If you just put everything together, the
car will not be as free as if you spend some time on "blueprinting"
things. You want to make sure the areas where the outdrive bearings
ride in the trans cases will not bind things up when they are
tightened down. A sharp hobby knife can be used to scrape the
area until things free up. Usually you only need to take a small
amount off. Just go slow. The same goes for the bearings that
the output shafts ride on. The main thing is to make thing feel
free. Each case can be put together and "spin-checked" before
you put everything together. This car is luckily very modular.
By the way the Teflon bearings are way better friction wise than
the rubber seals. It pays to get the FT or team car. 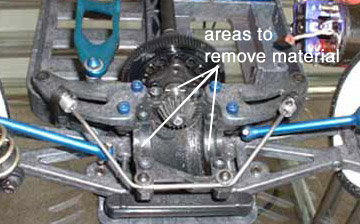
The bearing cap in front of the spur is also very important as
it is easily over tightened. The best way is to tighten one side,
making sure it remains free. Then do the same with the other side.
Tightening one side at a time helps to ensure you are not binding
the bearing. In fact, you do not need to go gorilla arm tightening
every screw on the car. You'll cut down on stripped out holes
and binding. If you have the plastic diffs, don't use any shims.
We have found out they aren't necessary. The metal diffs need
one, maybe two shims. One is usually best. The same goes for the
output shafts. I usually have about 2 shims on the shafts, but
you may need to see what works best for you. 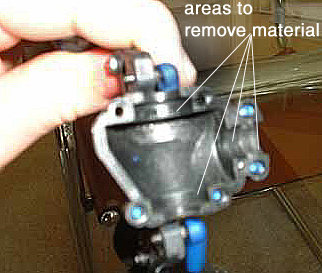
Reducing the number of shims helps to loosen up the drive train.
Obviously Associated needs to keep people from screwing their
cars up, so they recommend what will ensure the least number of
problems. This really is not the fastest however. Team CRC sells
shims that can be used on the CVD axles to keep them from floating
too much in thehubs. I like to put the shims on the outside (wheel
side) of the axle to keep the roll pin from contacting the face
of the bearing/hub.
Probably a bit anal, but whatever..
By now the drive train should spin very freely, so you can think
about countersinking the bottom of the car. Dremel sells a stone
bit, which can be used to take down the main part of the material.
You can then use an 82* countersink, which you can get from Sears
hardware dept. I have also used a Dremel bit made for something
else, but it appears to be an 82* bit also. (See pictures) I got
the countersinking idea from Mike
Lufaso's site.
Swaybars
are good for you car, and to make sure they stay put used thrust
washers come in handy. You can put them under the supplied swaybar
screws, and they are an almost perfect fit. It may be helpful
to shave down a bit of the outside of the trans case to make them
sit flat.
The steering rack can also be made a bit easier to get right.
On each post of the steering rack, a thin motor shim can be added
under the bottom bearing and on top of the top bearing. This allows
you to tighten the nuts down without binding up the steering.
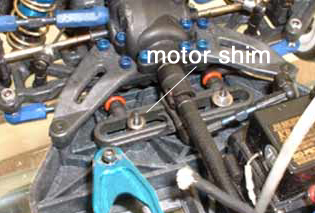
Anyway, I think I may have some more stuff on the TC3 soon, but
this will have to do for now.
|